Quality Assurance (QA) System Services
Quality assurance services can help identify long-term solutions to resolve recurring safety and quality concerns in manufacturing companies.
Your Trusted Partner
Quality Assurance (QA) System Services
QA/ QC Training: On-site factory training for quality control (QC) inspectors
Improving product quality must be done in the right way. We improve the way of working and checking efficiency through training.
How it's Work?
Providing training to employees at all levels on the QMS, including its principles, procedures, and documentation.
- How to check: Fabric, Accessories, Pattern, Cut panel, Sewing, Packing accuracy, final audit
- How to measure: Pattern, Garment
- How to determine the type of defect that exists in the product
Reporting system and SOP on all quality teams
With a Quality assistant, you can trust that your product is still under control and well developed in the manufacturing process.
Setting up the system and implementing a quality system in your factory.
Quality system setup: Implementing a one-stop quality system for manufacturers in the factory
Implementing a quality management system as a whole in the factory. Starting from the arrival of raw materials, production preparation, in the production process, to packing products that will be ready to ship. Implementation will be carried out according to the capacity and facilities and also the manpower available in the factory
How it's Work?
Start from audit your existing management systems and processes and provide you with a benchmark by issuing a comprehensive report on the condition of your system with advice relating to any weaknesses to help make them into strengths.
Implementation of a quality system with our professional quality will help you build a system starting from the raw material receiving system until finished garment ready to send.
Designed for Managers and employees who have responsibility for quality of product, systems and auditing, our courses provide all of the elements for individuals who are required to implement. and manage quality management system or for those in an existing role who simply require a refresher.
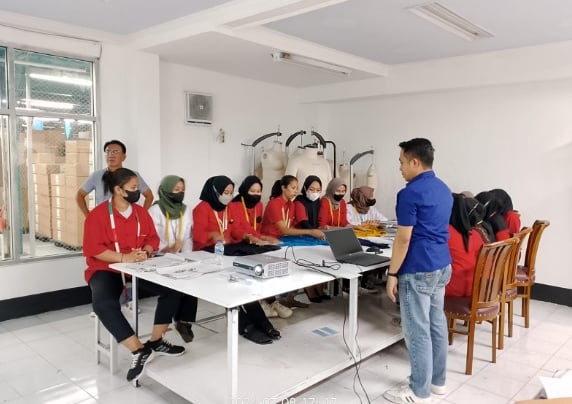
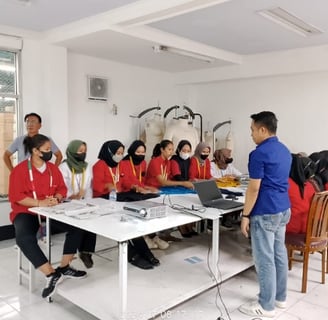
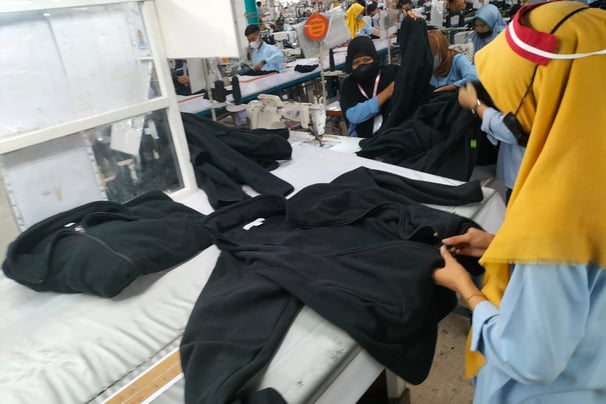
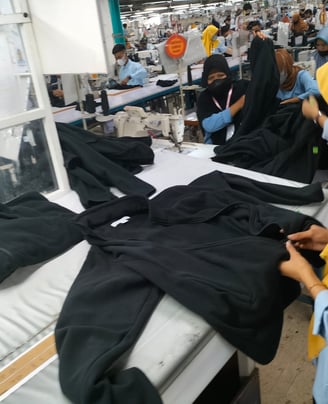

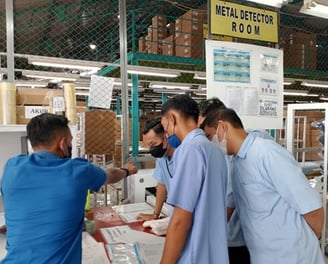
We declare we are – A team that has a function as an advisor and your executor to build and control, values-based idea coordination that is meaning promote cooperation, describe, react and execute. Fast and purposeful.
Delivering trusted consumer products starts with rigorous quality control, compliance checks, and sustainability practices.
The system implementation process will be assessed and evaluated and reported to management.
The implementation time will be determined from the initial audit results and based on the existing system, and the needs of factory management.
The training process will be carried out with an understanding of theory and practice
Training needs will be adjusted to the needs and results of the initial audit of existing QA / QC.
Client Feedback
Our clients appreciate our quality, dedication, and professional garment manufacturing services.
2needle transformed our ideas into reality with exceptional quality and attention to detail. Highly recommend their services for garment manufacturing and quality assurance!
Sarah Johnson
Bali, Indonesia
Working with 2needle has been a fantastic experience. Their team provided amazing support from design to production while ensuring high quality and consistency throughout the process.
Mark Taylor
Bali, Indonesia